Optimization of production processes and monitoring the condition of machinery in your company.
Continuous monitoring and control of the condition of machines along with their consumables results in increasing the efficiency of your company and reducing the costs associated with production downtime. Most often, the failure of one of the elements of the production line means that it must be completely shut down, which in turn generates huge costs. Thanks to our work, you will minimize this risk and optimize production processes.
Optimization of production processes in your company. Learn more!
Machine condition monitoring
Monitoring the condition allows for early detection and localization of emerging machine failures. This translates into proper planning of service activities and optimal utilization of the lifespan of important components. Sensors can be used to monitor any elements and factors to which machines are subjected.
Vibration monitoring and detection
Every machine generates vibrations during its operation. The stronger vibrations and their amplitude, the shorter the life of the machine and its consumables. This carries the risk of unplanned related downtime failure and maintenance costs.
Vibration sensors together with dedicated software allow
you to control these parameters and react to strong or irregular vibrations that threaten both the production processes as well as the machine itself.
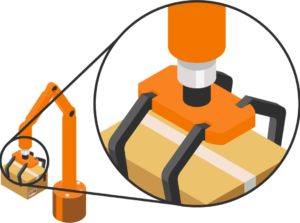
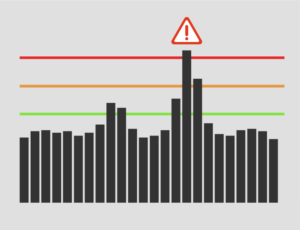
Measurements of the working parameters of the production machine
The goal of optimization is usually production variables such as machine operating hours, the number of processed parts/details, the frequency of replacing consumable parts, and tools used in the machining process (e.g., cutting), etc.
Condition of consumables
Thanks to our solutions, you can monitor
machine status and control the condition and wear of individual consumables. A failure of one of them during normal operation may result in damage to the other elements i.e. the production detail processed on a given machine or the production machine itself.
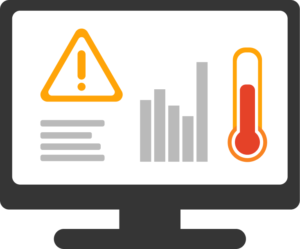
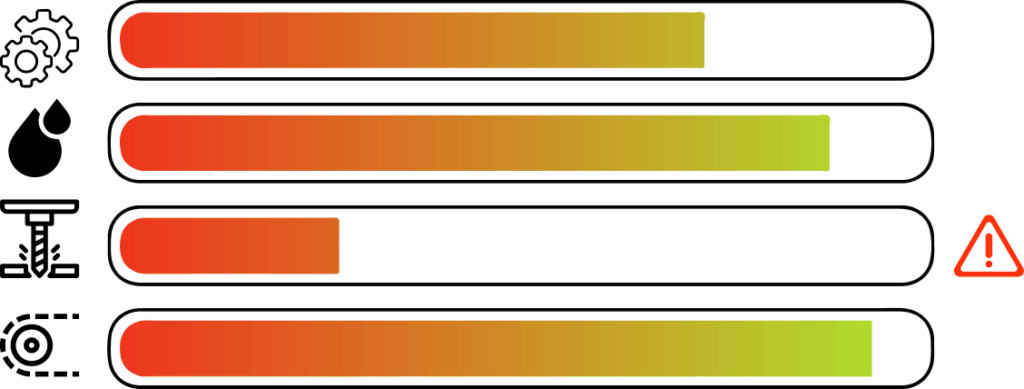
What can you gain
by working with us?
Supporting tools
for Maintenance Services
Stabilization of production capacity
Reducing unplanned downtime
Cost optimization
Implementation of new solutions
EU funding in joint projects
We create, implement and develop dedicated applications
Innovative projects for business
One of the largest projects in which we have been actively participating for many years is the Drivetrain Analyzer X-Tools program, which was created in cooperation with Siemens AG.
Dedicated industrial systems
We create and develop dedicated software to streamline the optimization of industrial processes.
Drivetrain Analyzer X-Tools - dedicated application
developed by Alfa-Net
CMS (ang. condition monitoring system)
Optimization of production processes
Industrial system for continuous monitoring of machine condition, supporting effective solutions to maintenance-related issues. It aids in equipment maintenance planning and production process optimization.
Drivetrain Analyzer X-Tools is a continuous monitoring system. It combines a robust hardware foundation with innovative IT solutions. The Drivetrain Analyzer X-Tools system has a modular character, thanks to which it has great possibilities of parameterization of its individual elements. It enables precise adjustment of the program to the specific needs of specific customers.
